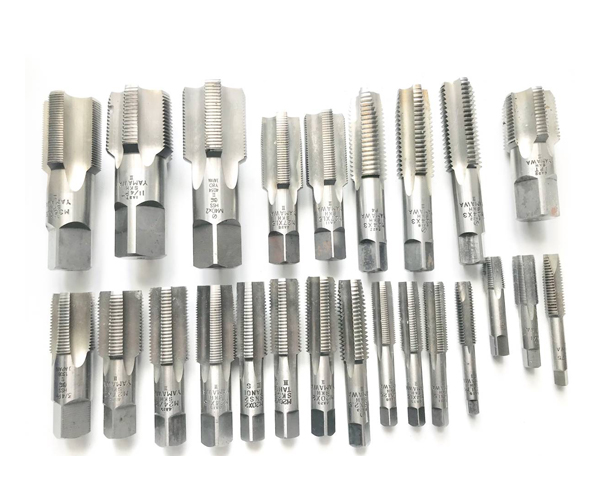
“The top of Yamawa technology, for tapping at ultra-high speed or under dry condition in respect of ISO14001”
HF ULTRA FAST series.
For ultra-high speed cutting. Having strengthened and high-precision shank for reduced run-out, HF taps run at up to 10 times higher speed than conventional taps, achieving dramatic reduction on cycle times and massive savings.
F FAST series.
Using the Fast taps, you can reduce the tapping costs thanks to a 3 times higher tapping speed. Fast taps are made of top quality HSSE, able to reduce the cutting pressure and to increase the tool breaking resistance.
HD DRY series.
HD series deliver consistent performance under such severe cutting condition as Dry tapping or Semidry tapping. Featuring an anti-wear and anti-welding surface treatment, HD series stand for high precision and outstanding tool life.
“The benefits of carbide available for tapping applications”
CT-FC – cast iron.
These taps are made of ultra-fine micrograin tungsten carbide; they show excellent wear resistance and high toughness, so they are recommend for mass-production threading.
MC-AD-CT – aluminium alloys.
For a better efficiency on blind hole tapping in such materials as aluminium die castings and aluminium alloy castings. These taps adopt ultra fine grain carbide with high wear resistance feature and TiAIN coating.
EH-CT – hardened steel 45~55HRC.
Ultra fine grain carbide alloys with superior wear resistance and shock resistance are adopted. By using the tap blanks in which both the run-out tolerance and the shank concentricity are improved, the high accuracy in screw threads can be obtained.
UH-CT – hardened steel 50~63HRC.
Suitable for tapping SKD die steels and pre-hardened steels which hardness ranges in 50-60 HRC (Maximum hardness 63 HRC).
“The latest development as accuracy and performance”
VA+ stainless steel.
It is specifically designed to machine stainless steel, granting a 3-times longer tool life than conventional taps.
AU+ universal application.
The Yamawa universal tap, for high-performance on a wide range of materials (steel, alloy steel, stainless, aluminium).
“The first choice for blind hole”
Spiral fluted taps are recommended for blind hole tapping, as the flute helix efficiently ejects chips out of the hole. They are most suitable to machine blind holes on medium- and long-chip materials. Thanks to their features, they deliver superior performance in interrupted tapping and in the machining of holes with slots.
“The conventional geometry for through holes”
Spiral pointed taps are suitable to machine through holes, and deliver consistent performance thanks to their rather strong design.
“The most efficient geometry to machine through holes”
Left-hand spiral flutes represent a development of spiral-pointed taps, achieving smoother chip ejection and control. This results in longer tool life, higher performance consistency, and higher cutting speed. This geometry applies to high-end Yamawa taps for through holes.
“The basic tap style”
These taps usually produce very small chips, thus being suitable to machine both blind and through holes. Straight-fluted taps represent the first choice for hand-tapping.
“Tapping without chips”
These taps produce threads by deforming the material, thus without any chips. They are suitable for blind and through holes, and their field of application has grown wider, including now aluminium , steel up to 32 HRC, and stainless. Thread forming taps do not have flutes for ejecting chips but may have grooves for oil supply.